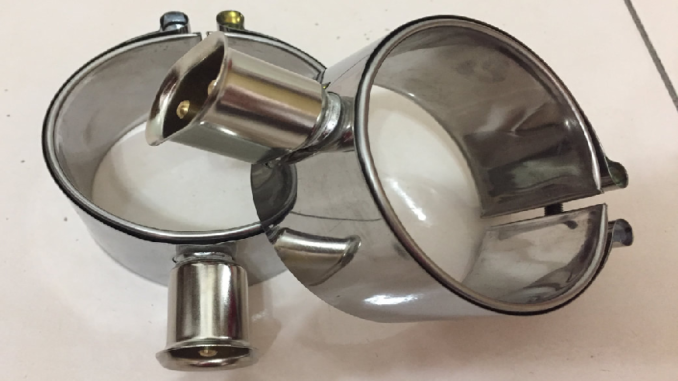
The band heater is one of the most common types of heaters used in industrial processes.Band heaters are generally found in applications such as metal fabrication and welding, plastic forming, brazing and sintering; parts hardening; paint baking; shrink fitting; circuit board soldering; ceramics processing; thermal spraying and many other processes.
The band heater works by passing electricity through the heating element, which is wrapped on a spool. The heat is transferred to the product via radiation and conduction. The amount of heat transferred depends on the thickness, length of the band heater and applied voltage.
Band heaters are available in either resistive or inductive types. Resistive band heaters transfer electrical energy to thermal energy via resistance, conduction and radiation. Resistive band heaters are available in a wide variety of different materials such as Nichrome, Kanthal, flexible nichrome wire, silicone rubber and even ceramic insulators.
Inductive band heaters utilize the principle that when current is passed through a coil of wire, a magnetic field is created. As the magnetic field formation moves down the length of the coil it induces an electrical current in each successive turn. The result is that energy loss due to eddy currents are minimized. The induced current or back emf then generates heat along the entire band heater by induction heating, which dissipates via radiation and conduction. Inductive band heaters are available in a variety of materials such as copper, aluminum or alloy wire.
Types Of Band Heaters:
Band heater types include: Conventional Band Heaters – A conventional band heater provides even surface temperature throughout the entire length of the heating element, whereas a special application band heater may have a center region or hot spot. Conventional band heaters can be supplied as one continuous piece, for wrapping around large irregularly shaped objects such as pipes and cylinders, or as short sections with an adhesive backing to apply to flat objects like drums and tanks.
Special application band heaters are typically available only in limited standard sizes, which means manufacturing custom lengths is difficult. This can be an issue if the need arises for a non-standard size, or when replacing sections of band heater already in place. Some typical special applications include: – Band heaters with hot spots to directly apply heat to mechanical components such as motors, blowers, bearings and gears – Band heaters where the entire length is not required to be at the same temperature – Band heaters with a center section that is hotter than the outer zones
Special application band heaters can also be supplied in coiled form. Coiled band heaters often provide superior efficiency because there is less energy loss due to eddy currents and they offer flexibility when it comes to different shapes and sizes of objects to be heated.
Coiled band heaters can also reduce installation and manufacturing costs because:
– No insulation is required because the heating element does not come in direct contact with the object – Coiling reduces weight allowing for smaller, less expensive equipment such as manual or pneumatic feeders – Coiled band heaters are flexible which allows them to be used on irregularly shaped objects
Coiled band heaters are particularly useful in applications where the heating element must wrap around a corner. Large coiled band heaters can also be unwound as they are fed into place, eliminating the need for retraction mechanisms or transfer lines.
Leave a Reply
You must be logged in to post a comment.